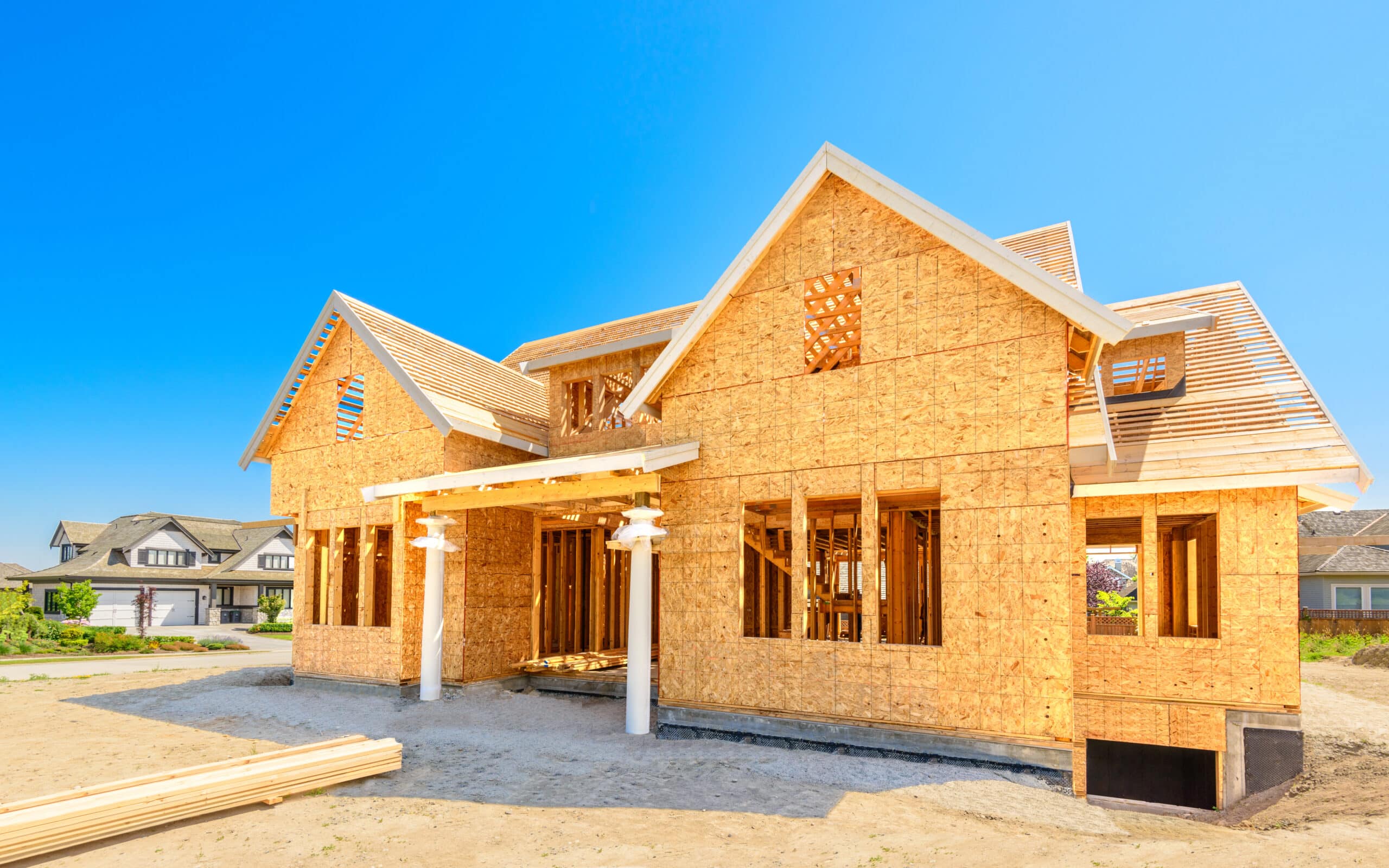
Homes are being built faster than ever. This makes it more important for “new build” buyers to have the work inspected. Homes and buildings must be constructed according to local, state, and federal guidelines. All these mandates only ensure the minimum standards for the homes and buildings to be habitable. This can leave a lot of room for subpar construction or corners being cut, especially when you’ve never seen what has been covered up by drywall. It is often too late to find possible defects after the home is completed, so having a pre-drywall inspection helps ensure quality work throughout the process.
A pre-drywall inspection covers framing/pre-drywall elements in the home. Your inspector will come out at this crucial point in the building process before defects can be covered up by insulation and drywall. This is the critical point to have changes made. Your interactive report will list out the issues with visuals to show exactly where the concerns lie. With the report in hand, you will be able to have a more productive conversation with your builder. This inspection should give you peace of mind that a solid foundation is in place before the rest of your home is built.
When your RHI inspector comes to your home to conduct an inspection, your home should be dried in. This means the roof should be installed. Your home should have all its doors and windows, and the house should be wrapped with a weather-tight barrier. All the plumbing, electrical, and HVAC components should also be in place. Your inspector will check all these areas. Your inspector will also check for properly bolted sill plates, over spanned members, inadequate roof supports, underbuilt bearing walls, improper notching and boring, severed plates, damaged joists, added support strips for your cabinets, improper fire stops, etc.
We recommend this type of inspection because of the concerns we have encountered when inspecting during pre-drywall. Some examples of issues we have found during pre-drywall inspections are decking nails shot through the electric panel and into one of the main conductors. These nails being improperly nailed into the panel would have caused the electric panel itself to become hot when energized. We have also found improperly drilled holes for electric circuits. These holes were drilled to close to the outer edge of the 2×4 stud. When this happens a metal plate has to be added to prevent a drywall screw from coming into contact with the wire within.
Other issues include improperly fastened cabinet nailers. These boards are put in place to help support cabinets with they are fully loaded with dishes. We have found improperly installed headers over doorways. When you install a window or door, the frame has to be built in a way to carry the load of the home around the window or door. This prevents the door or window from getting pinched by the weight of the home. We have also encountered improperly set tub surround. When setting a bathtub or shower surround, the surround should be set in concrete or a high dense spry foam. The surround has feet that should be leveled when being set. If the feet are not all resting on the ground, the fiberglass can crack much more easily if someone is standing or sitting in the tub. If the surround is set in concrete or high-dense foam, it is also less likely to crack if a shampoo bottle or some other hard objects were dropped.
RHI’s pre-drywall inspection can give you peace of mind that you are getting what you paid for in a home. Getting a pre-drywall inspection is just smart if you are building. When you are putting the amount of money it takes to build into a home, you want it to be right. You want it to be safe. The examples we discussed above are just some of the issues we have encountered. When several crews are hired to come in and complete different jobs on your home, you want to make sure the caliber of work is what the builder promised. RHI can help you know that your home was built properly, and it is a safe place for you and your loved ones.
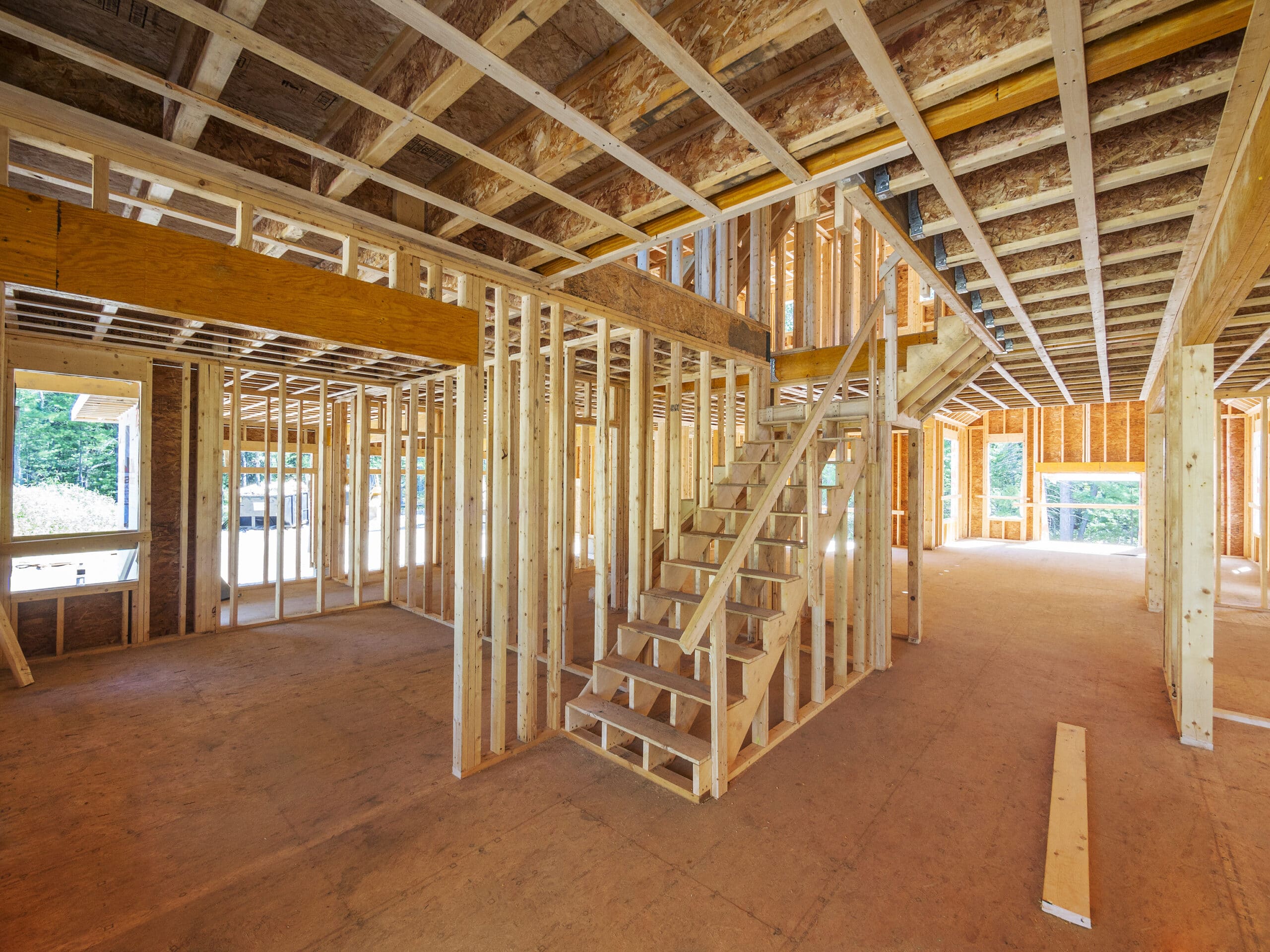